Французский институт солнечной энергетики INES разработал новые фотоэлектрические модули из термопластов и натуральных волокон европейского происхождения, таких как лен и базальт.Ученые стремятся уменьшить воздействие солнечных батарей на окружающую среду и вес, одновременно улучшая переработку.
Панель из переработанного стекла спереди и льняной композит сзади.
Изображение: ГД
Из журнала PV France.
Исследователи из Национального института солнечной энергии Франции (INES) – подразделения Французской комиссии по альтернативной энергетике и атомной энергии (CEA) – разрабатывают солнечные модули с новыми биологическими материалами на передней и задней сторонах.
«Поскольку выбросы углекислого газа и анализ жизненного цикла теперь стали важными критериями при выборе фотоэлектрических панелей, поиск материалов станет решающим элементом в Европе в ближайшие несколько лет», — сказал Анис Фуини, директор CEA-INES. в интервью журналу PV France.
Од Дерье, координатор исследовательского проекта, сказала, что ее коллеги изучили различные уже существующие материалы, чтобы найти тот, который мог бы позволить производителям модулей производить панели, которые улучшают производительность, долговечность и стоимость, одновременно снижая воздействие на окружающую среду.Первый демонстратор состоит из солнечных элементов с гетеропереходом (HTJ), интегрированных в цельнокомпозитный материал.
«Лицевая сторона изготовлена из полимера, наполненного стекловолокном, что обеспечивает прозрачность», — сказал Дерье.«Задняя сторона изготовлена из композита на основе термопластов, в который интегрировано переплетение двух волокон, льна и базальта, что обеспечит механическую прочность, а также лучшую устойчивость к влажности».
Лен поставляется из северной Франции, где уже присутствует вся промышленная экосистема.Базальт добывается в других странах Европы и ткут промышленный партнер INES.Это снизило выбросы углекислого газа на 75 граммов CO2 на ватт по сравнению с эталонным модулем той же мощности.Вес также был оптимизирован и составляет менее 5 килограммов на квадратный метр.
«Этот модуль предназначен для интеграции фотоэлектрических систем на крыше и зданий», — сказал Дерье.«Преимущество состоит в том, что он имеет естественный черный цвет и не требует использования заднего листа.С точки зрения переработки, благодаря термопластам, которые можно переплавлять, разделение слоев также становится технически проще».
Модуль можно сделать без адаптации текущих процессов.Дерье сообщил, что идея состоит в том, чтобы передать технологию производителям без дополнительных инвестиций.
«Единственное, что необходимо — это иметь морозильные камеры для хранения материала, а не для запуска процесса сшивки смолы, но большинство производителей сегодня используют препрег и уже оборудованы для этого», — сказала она.
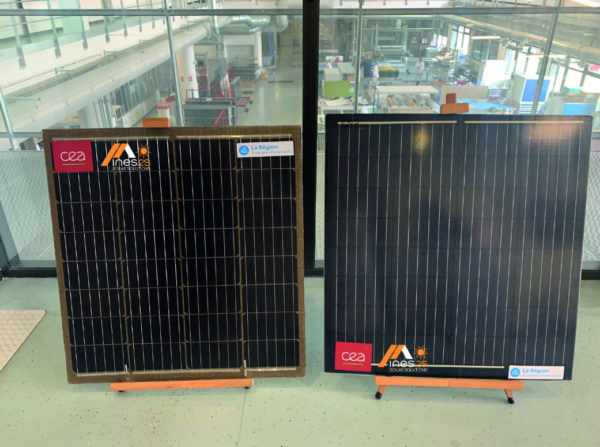
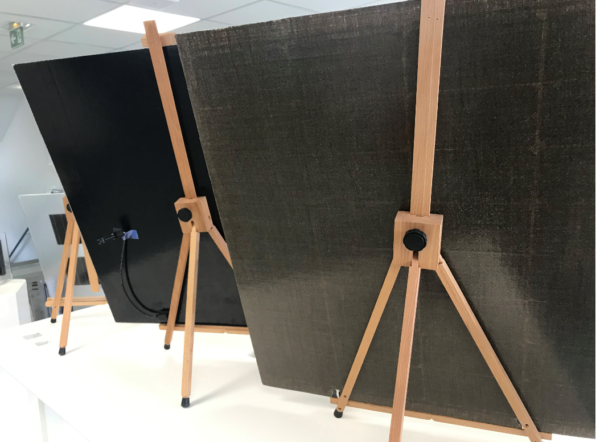
«Мы работали над второй жизнью стекла и разработали модуль, состоящий из повторно использованного стекла толщиной 2,8 мм, полученного из старого модуля», — сказал Дерье.«Мы также использовали термопластичный герметик, который не требует сшивания и поэтому его будет легко перерабатывать, а также термопластичный композит с льняным волокном для обеспечения устойчивости».
Безбазальтовая задняя сторона модуля имеет натуральный льняной цвет, что может быть эстетически интересно для архитекторов, например, с точки зрения интеграции с фасадом.Кроме того, инструмент расчета INES показал снижение углеродного следа на 10%.
«Сейчас крайне важно подвергнуть сомнению цепочки поставок фотоэлектрических систем», — сказал Жуини.«Поэтому с помощью региона Рона-Альпы в рамках Международного плана развития мы начали искать игроков за пределами солнечной отрасли, чтобы найти новые термопласты и новые волокна.Мы также подумали о нынешнем процессе ламинирования, который очень энергозатратен».
Между этапами повышения давления, прессования и охлаждения ламинирование обычно длится от 30 до 35 минут при рабочей температуре от 150 до 160 C.
«Но для модулей, в которых все чаще используются экологически чистые материалы, необходимо преобразовывать термопласты при температуре от 200 до 250 C, зная, что технология HTJ чувствительна к нагреву и не должна превышать 200 C», — сказал Дерье.
Научно-исследовательский институт сотрудничает с французской компанией Roctool, специализирующейся на индукционной термокомпрессии, чтобы сократить время цикла и изготавливать формы в соответствии с потребностями клиентов.Вместе они разработали модуль с задней поверхностью из термопластичного композита полипропиленового типа, в который были интегрированы переработанные углеродные волокна.Лицевая сторона изготовлена из термопластика и стекловолокна.
«Процесс индукционной термокомпрессии Roctool позволяет быстро нагревать две передние и задние пластины без необходимости достижения температуры 200 C в сердцевине ячеек HTJ», — сказал Дерье.
Компания утверждает, что инвестиции ниже, а время цикла процесса может составить всего несколько минут при меньшем расходе энергии.Технология ориентирована на производителей композитов, чтобы дать им возможность производить детали разных форм и размеров, используя при этом более легкие и прочные материалы.
Время публикации: 24 июня 2022 г.