Французский институт солнечной энергии Ines разработал новые фотоэлектрические модули с термопластиками и натуральными волокнами, полученными в Европе, таких как льня и базальт. Ученые стремятся уменьшить окружающую среду и вес солнечных батарей, одновременно улучшая переработку.
Переработанная стеклянная панель на передней части и льняная композит на задней части
Изображение: Gd
От PV Magazine France
Исследователи из Франции Национального института солнечной энергии (INES)-подразделения французской альтернативной энергии и комиссии по атомной энергии (CEA)-разрабатывают солнечные модули с новыми биографическими материалами на передней и задней сторонах.
«Поскольку углеродный след и анализ жизненного цикла теперь стали важными критериями при выборе фотоэлектрических панелей, поиск материалов станет важным элементом в Европе в ближайшие несколько лет»,-сказал Анис Фуини, директор Cea-Ines , в интервью PV Magazine France.
Ауде Дерриер, координатор исследовательского проекта, сказала, что ее коллеги рассмотрели различные материалы, которые уже существуют, чтобы найти тот, который мог бы позволить производителям модулей производить панели, которые улучшают производительность, долговечность и стоимость, одновременно снижая воздействие на окружающую среду. Первый демонстратор состоит из гетеропереходных (HTJ) солнечных элементов, интегрированных в всекомпозитный материал.
«Передняя сторона изготовлена из полимера, наполненного стекловолокном, который обеспечивает прозрачность»,-сказал Дерриер. «Задняя сторона изготовлена из композита на основе термопластов, в которых было интегрировано ткачество двух волокон, льна и базальта, что обеспечит механическую прочность, но также и лучшую устойчивость к влажности».
Линь получен из северной Франции, где уже присутствует вся промышленная экосистема. Базальт поставляется в других местах Европы и состоится промышленным партнером Ines. Это уменьшило углеродный след на 75 граммов CO2 на ватт по сравнению с эталонным модулем той же мощности. Вес также был оптимизирован и составляет менее 5 килограммов на квадратный метр.
«Этот модуль предназначен для PV и интеграции на крыше», - сказал Дерриер. «Преимущество заключается в том, что он естественно черный цвет, без необходимости в листе. С точки зрения утилизации, благодаря термопластикам, которые можно переполнено, разделение слоев также технически проще ».
Модуль может быть изготовлен без адаптации текущих процессов. Дерриер сказал, что идея состоит в том, чтобы передавать технологию производителям без дополнительных инвестиций.
«Единственный императив-иметь морозильные камеры для хранения материала, а не запустить процесс сшивки смолы, но большинство производителей сегодня используют PREPREG и уже оснащены для этого»,-сказала она.
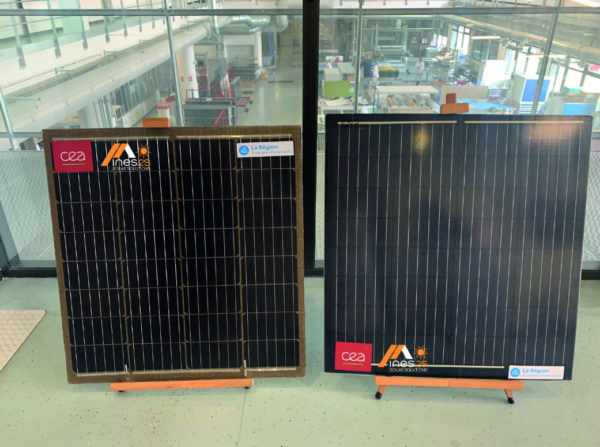
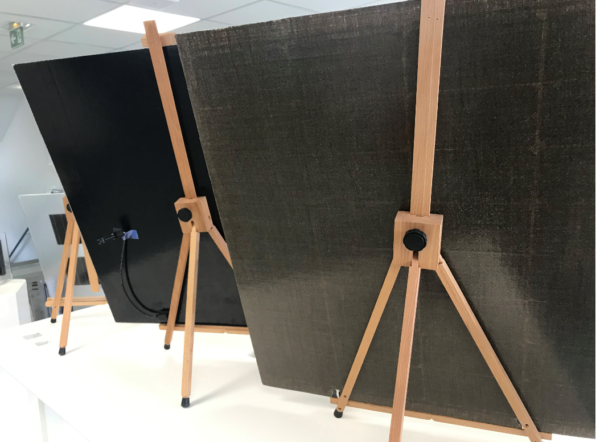
«Мы работали над второй жизнью стекла и разработали модуль, состоящий из повторно используемого 2,8 мм стекла, который поступает из старого модуля», - сказал Дерриер. «Мы также использовали термопластичный инкапсусант, который не требует сшивки, который, следовательно, будет легко переработать, и термопластичный композит с льняным волокном для сопротивления».
Задняя поверхность модуля без базальта имеет естественный цвет льна, который, например, может быть эстетически интересным для архитекторов с точки зрения интеграции фасада. Кроме того, инструмент расчета INES показал сокращение углеродного следа на 10%.
«В настоящее время необходимо подвергнуть сомнению фотоэлектрические цепочки поставок», - сказал Жуини. «С помощью региона Rhône-Alpes в рамках Международного плана развития мы поэтому мы пошли искать игроков за пределами солнечного сектора, чтобы найти новые термопластики и новые волокна. Мы также подумали о текущем процессе ламинирования, который очень энергоемкий ».
Между давлением, нажатием и фазой охлаждения ламинирование обычно длится от 30 до 35 минут, причем рабочая температура составляет от 150 до 160 с.
«Но для модулей, которые все чаще включают эко-разработанные материалы, необходимо трансформировать термопластики со скоростью от 200 до 250 ° С, зная, что технология HTJ чувствительна к тепло и не должна превышать 200 ° С»,-сказал Дерриер.
Научно-исследовательский институт объединяется со специалистом по индукционной термокомпрессии, базирующемуся в Франции Roctool, чтобы сократить время цикла и создавать формы в соответствии с потребностями клиентов. Вместе они разработали модуль с задней поверхностью, изготовленной из термопластичного композита полипропилена, в который были интегрированы переработанные углеродные волокна. Передняя сторона изготовлена из термопластов и стекловолокна.
«Процесс индукции Roctool индукционной термокомпрессии позволяет быстро нагреть две передние и задние пластины, не достигая 200 ° C в ядре клеток HTJ», - сказал Дерриер.
Компания утверждает, что инвестиции ниже, и процесс может достичь времени цикла всего за несколько минут, используя меньше энергии. Технология предназначена для производителей композитов, чтобы дать им возможность производства частей различных форм и размеров, одновременно интегрируя более легкие и более прочные материалы.
Время сообщения: июнь-24-2022